مقدمه
بهبود عمر خستگی سازهها: راهکارهای مکانیکی و حرارتی
سازههایی که در حین کار تحت ارتعاش و بارگذاریهای متناوب قرار میگیرند، بهطور جدی از خرابی ناشی از خستگی رنج میبرند. در طول تاریخ، به دلیل اهمیت افزایش عمر سازهها، اثرات روشهای مکانیکی، حرارتی و پینینگ بر بهبود خصوصیات مواد بررسی شده و همچنان در حال توسعه است. اختراع هواپیما نقطه عطفی در مطالعات خستگی بود؛ چرا که در این صنعت نیاز به مواد با عملکرد بالا، بدون محدودیتهای مرتبط با خستگی، الزامی محسوب میشد و معرفی مواد غیر فلزی نیز افقهای جدیدی در این زمینه گشود.
عوامل مؤثر بر عمر خستگی
عمر خستگی مواد به چندین عامل اساسی وابسته است:
خواص مکانیکی: مقاومت ماده در برابر تنش و تغییر شکل.
پرداخت سطح: کیفیت پرداخت سطح نقش کلیدی در جلوگیری از شروع ترک دارد.
محیط اطراف: شرایط محیطی مانند دما، رطوبت و عوامل خور (corrosive).
نوع و مقدار بار: بارهای متناوب، تنشهای متمرکز (مثلاً در اتصالات پرچ شده) و تاثیرات ناشی از آنها.
هنگامی که ترک در ماده ظاهر میشود، سرعت انتشار آن به ریزساختار ماده بستگی دارد. با اعمال تنشهای فشاری به سطح سازه، میتوان از شروع ترک جلوگیری کرده و سرعت رشد آن را به تأخیر انداخت.
کاربرد در صنایع مختلف
در سازههای هواپیما، اتصالاتی همچون پوستهها و دندهها به دلیل داشتن پرچ، نقاط متمرکز تنش محسوب میشوند که میتوانند منجر به آغاز آسیب خستگی شوند. استفاده از روشهای پیشگیرانه برای به تأخیر انداختن شروع و رشد ترکهای خستگی، هم امنیت سازه را افزایش میدهد و هم عمر مفید آن را بهبود میبخشد. این رویکرد نه تنها در صنعت هوافضا بلکه در خودروسازی، حمل و نقل و صنایع ماشینآلات متحرک اهمیت فراوان دارد.
روشهای بهبود عمر خستگی
برای افزایش مقاومت مواد در برابر خستگی، تکنیکهایی بهکار گرفته میشوند که موجب تغییر خواص سطحی مانند اندازه دانه، ریزسختی، زبری و کاهش عیوب سطحی میشوند. این روشها در دو دسته کلی قرار میگیرند:
۱. عملیات مکانیکی
شات پینینگ: ایجاد تنش فشاری در سطح ماده.
نورد سطحی: پالایش سطح و بهبود ترکیب سطحی.
خودکار فرتاژ و لایهبرداری لیزری: جهت حذف عیوب سطحی و افزایش سختی سطحی.
۲. عملیات حرارتی
کربورسازی و نیتریدینگ: تغییر در ترکیب سطحی بهمنظور ایجاد سختی و مقاومت بیشتر.
سخت شدن شعله و سخت شدن القایی: بهبود خواص مکانیکی و افزایش مقاومت در برابر سایش و خستگی.
حذف تنشهای کششی ناشی از جوشکاری
تنشهای کششی باقیمانده در اثر فرآیندهای جوشکاری میتوانند به عنوان عامل مهمی در ابتلا به خرابی خستگی سازهها شناخته شوند. به همین منظور، تکنیکهایی بهوجود آمدهاند که این تنشها را از بین برده و در نتیجه عمر خستگی را افزایش میدهند. از جمله این روشها میتوان به درمان ضربه التراسونیک (UIT) اشاره کرد که با پر کردن شکافهای باقیمانده، موجب بهبود عملکرد سازه میشود.
با استفاده از این رویکردهای جامع و ترکیب روشهای مکانیکی و حرارتی، افزایش عمر و عملکرد بهینه سازههای صنعتی تضمین شده و امنیت سیستمها در صنایع مختلف از جمله هوافضا، خودروسازی و حمل و نقل به طور چشمگیری ارتقا مییابد.
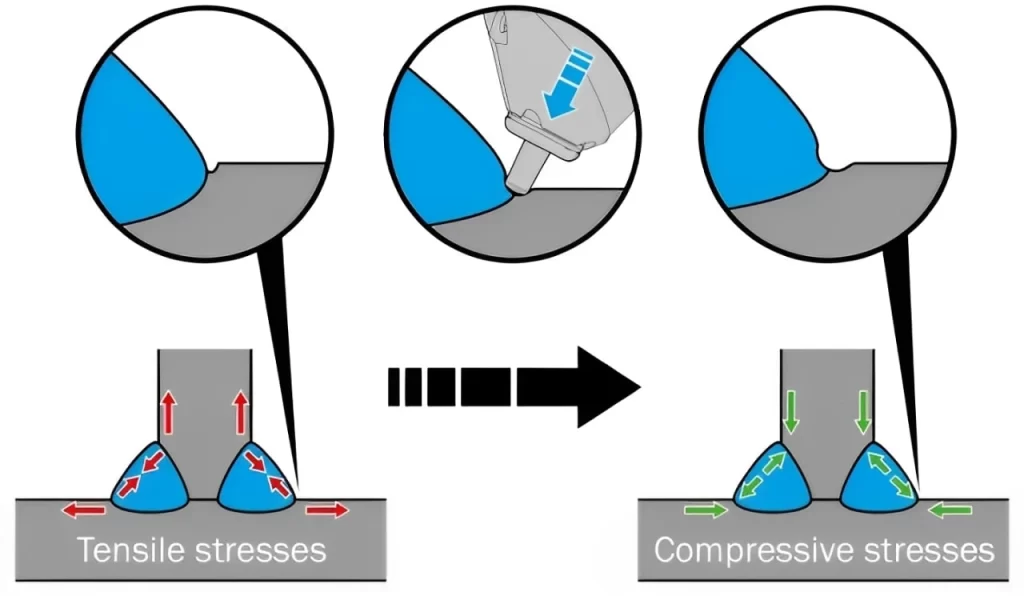
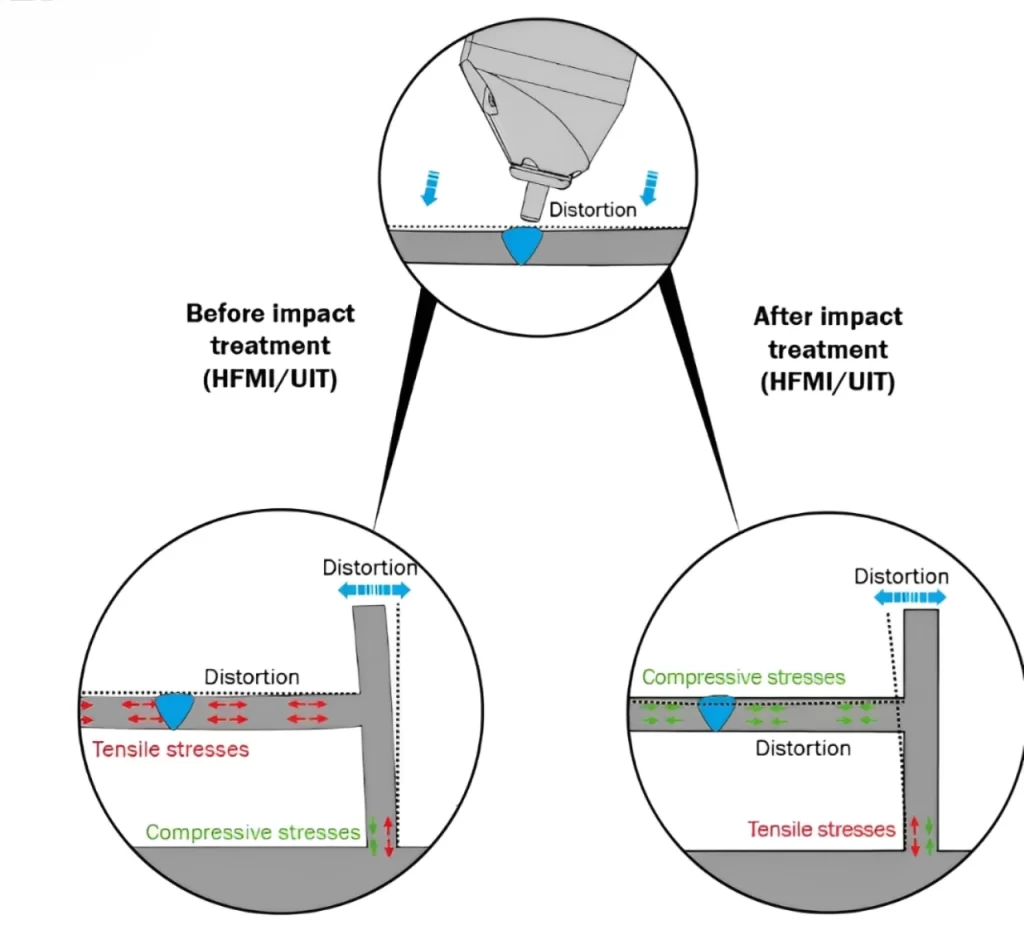
تاریخچه
روش درمان ضربه التراسونیک (UIT) در روسیه در اوایل دهه 1970 توسعه یافت و نشاندهنده یک پیشرفت چشمگیر در طراحی و اجرای روشهای بهبود مقاومت سازهها در برابر خستگی بود. این تکنیک به دلیل دستکاری دستی آسان و حمل و نقل تجهیزات، مزایای بسیاری نسبت به سایر روشهای مشابه ارائه داد.
ویژگیها و مزایای روش UIT
دستکاری و حمل تجهیزات به صورت دستی:
قابلیت استفاده دستی از تجهیزات UIT به اپراتورها این امکان را میدهد که به بخشهای دشواری از سازه دسترسی پیدا کنند که روشهای دیگر دسترسی به آنها را فراهم نمیکنند.کاهش خطرات فیزیکی:
در مقابل روشهایی مانند استفاده از صدا، ارتعاشات قوی، پرتابهها و لیزرها که در طول زمان ممکن است برای سلامتی اپراتورها خطر ایجاد کنند، UIT خطرات فیزیکی را به طور قابلتوجهی کاهش میدهد.کاهش تنشهای پسماند جوشکاری:
UIT به عنوان یک تکنیک معرفیشده برای کاهش تنشهای پسماند ناشی از جوشکاری در زیردریاییهای نیروی دریایی روسیه به کار گرفته شد و از این طریق تغییر شکلهای ناشی از فرآیند جوشکاری اصلاح گردید.
کاربرد UIT در حوزههای مختلف
زیردریاییهای نظامی
روش UIT ابتدا با موفقیت در مناطقی که در معرض شکستگی ناشی از خستگی بودند، برای فولادهای مورد استفاده در ساخت زیردریاییها به کار گرفته شد. این موفقیت منجر به بهبود خواص زیر شد:
افزایش استحکام خستگی:
بهبود مقاومت سازه در مقابل شکستگیهای مرتبط با خستگی.مقاومت در برابر خستگی در دمای پایین:
افزایش عملکرد سازهها در شرایط محیطی سخت و دماهای پایین.مقاومت در برابر خوردگی:
بهبود عملکرد و طول عمر سازه در محیطهای خور corrosive.
سایر آلیاژها
پس از موفقیت اولیه در زیردریاییها، روش UIT در آلیاژهای تیتانیوم، برنز و آلیاژهای آلومینیومی نیز به کار گرفته شد. این گسترش کاربرد باعث شد که از نظر:
کاهش هزینهها
صرفهجویی در زمان
کاهش ریسک فیزیکی برای اپراتورها
مزایای مهمی حاصل شود.
نکات و چالشهای موجود
با وجود موفقیتهای به دست آمده، اثرات فرآیند UIT بر روی مواد جوش داده شده هنوز به طور کامل شناخته نشده است. پژوهشهای بیشتر در این زمینه نیازمند بررسی دقیق تأثیرات فرآیند بر روی ساختار و خواص مواد پس از جوشکاری میباشد.
درمان ضربه ای التراسونیک (UIT)
بهبود عمر خستگی آلیاژهای آلومینیوم در وسایل نقلیه هوافضا با استفاده از روش UIT
آلیاژهای آلومینیوم بهعنوان یکی از مواد اصلی در ساخت وسایل نقلیه هوافضا به دلیل سبکی و مقاومت مکانیکی بالا به طور گسترده مورد استفاده قرار میگیرند. این مواد تحت بارهای چرخهای ناشی از عملکرد مداوم قرار دارند که میتواند باعث تغییرات مخرب در ساختار آنها شده و شرایط را برای شروع ترک و شکستن سازه مهیا کند.
اهمیت بهبود عمر خستگی در آلیاژهای آلومینیوم
بارهای چرخهای و تنشهای وارد بر آلیاژهای آلومینیوم در هوافضا ممکن است موجب تغییرات قابل توجهی در:
ریزش ساختاری مواد
افزایش مستعد بودن به شروع ترک
تسریع روند شکست سازه
شود. به همین جهت، بهبود فرآیندهای عملکردی این مواد از نظر مقاومت در برابر خستگی اهمیت ویژهای دارد.
روش درمان ضربه التراسونیک (UIT)
روش UIT یک راهکار تحقیقاتی پیشرفته است که در طی سالیان گذشته در مناطق جوشکاری بر روی مواد مختلف مانند فولاد، آلیاژهای تیتانیوم، آلیاژهای آلومینیوم و برنز با موفقیت بهکار گرفته شده است. این روش تاثیرات مثبتی بر بهبود عمر خستگی داشته و از ویژگیهای آن میتوان به نکات زیر اشاره کرد:
تغییرات در ریزساختار
ریزش ریزسختی و زبری:
فرآیند UIT باعث ایجاد تغییراتی در ریزساختار سطح ماده شده و میزان ریزسختی و زبری آن را کنترل میکند.تنظیم تنشهای پسماند:
پارامترهای مختلف UIT برای کنترل و کاهش تنشهای پسماند باقیمانده در سطح جوشکاری به کار گرفته میشوند. این کاهش تنش باعث افزایش مقاومت خستگی میشود.
ویژگیهای فرآیند UIT
طراحی سیستم با سه فرورفتگی آزاد:
در این روش از سه سوراخ خط راهنمای با آرایش خطی بهره گرفته میشود که با ایجاد فرورفتگیهای آزاد به صورت سوزنی، تأثیر قابلتوجهی بر سطح ماده داشته و نتایج مثبتی از لحاظ بهبود خواص مکانیکی حاصل میشود.تحریک پالس مدولاسیون فرکانس رزونانس:
فرورفتگیها در امتداد محورهای خود طبق فرکانس معین تحریک میشوند که موجب تغییر شکلهای میکرو و کاهش تنشهای باقیمانده در جوشکاری میگردد.
اثرات UIT در بهبود عمر خستگی
مطالعات نشان میدهند که روش UIT در اتصالات جوشی فولادی نسبت به سایر روشهای مانند پینینگ با چکش، شاتپینینگ، سوزنپینینگ و پانسمان TIG موفقیت چشمگیری داشته است؛ بهطوریکه:
افزایش مقاومت خستگی تا 120 درصد در اتصالات جوشی فولادی گزارش شده است.
در آلیاژهای آلومینیوم افزایش عمر خستگی به میزان حدود 80 درصد مشاهده شده است.
این بهبودها نتیجه کاهش ناپیوستگیهای ریز در نوک جوش، تغییر شکل پلاستیک و بهبود ساختار میکرو است که در نهایت به افزایش دوام و امنیت سازه منجر میشود.
با استفاده از روش UIT، صنعت هوافضا قادر است عمر مفید و عملکرد آلیاژهای آلومینیوم را به طور قابلملاحظهای افزایش دهد؛ از کاهش هزینهها و زمان پردازش تا بهبود ایمنی اپراتورها، این تکنیک به عنوان یکی از نوآورانهترین روشها در مبارزه با اثرات مخرب بارهای چرخهای و تنشهای باقیمانده شناخته میشود.
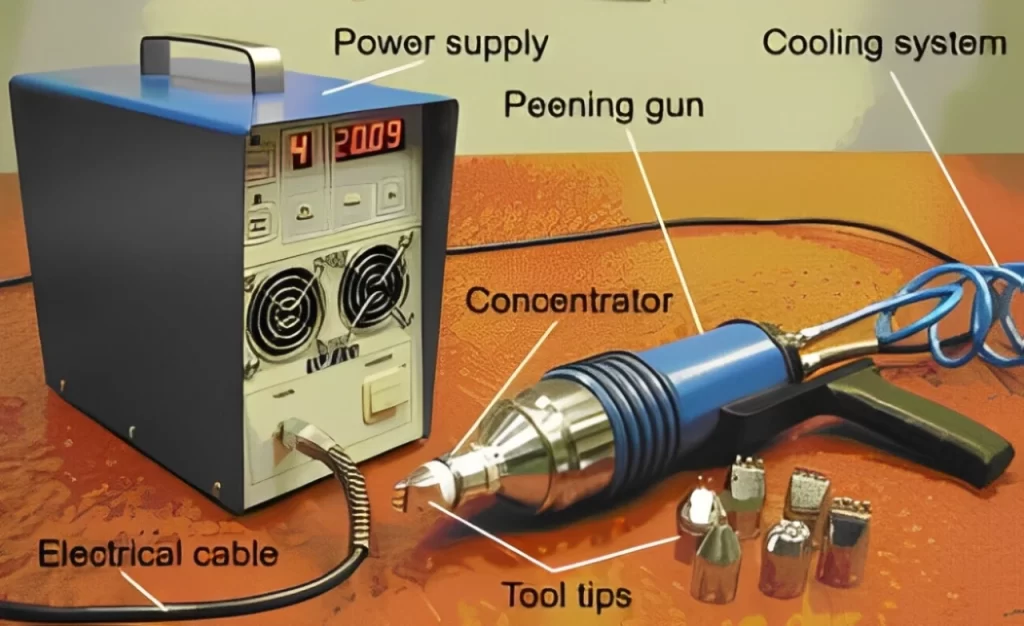
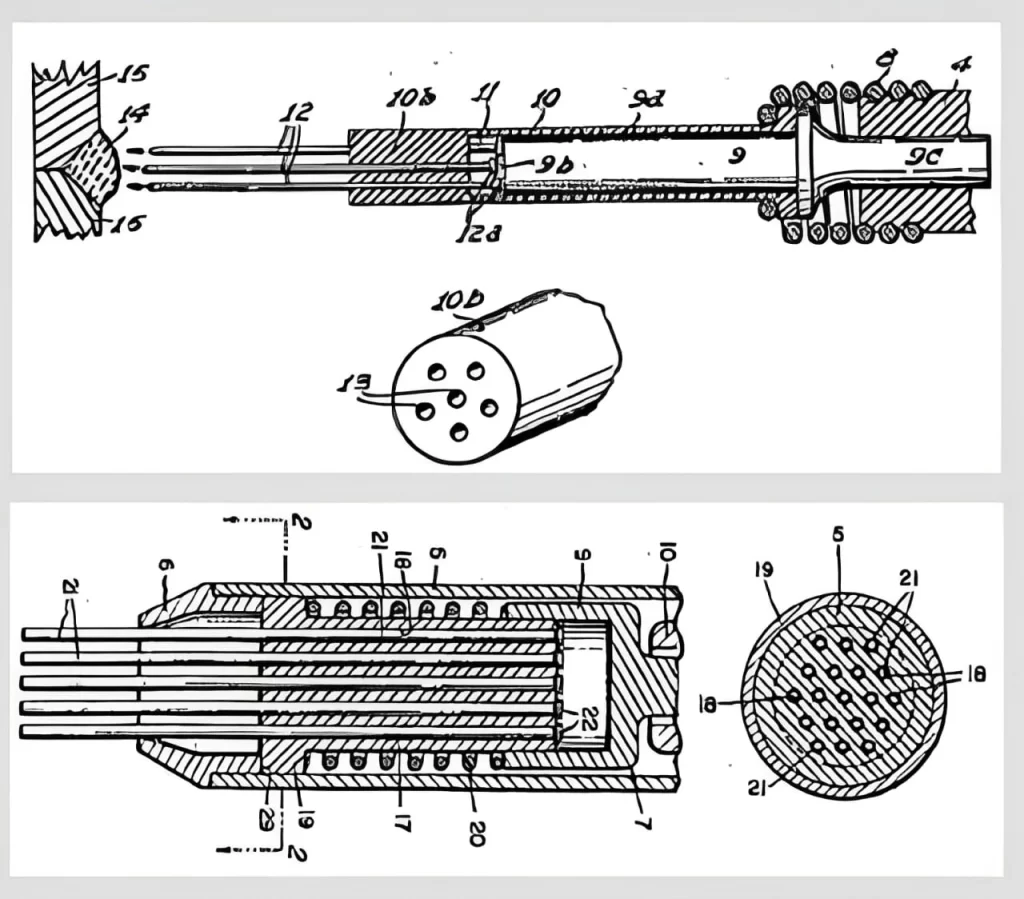
درمان سطحی
همانطور که پیشتر بیان شد، تنشهای موجود در سازهها به روشهای مختلفی ایجاد میشوند؛ اما از میان این روشها، مواردی وجود دارند که علاوه بر سادگی اجرا و هزینهی پایین، نتایج بهینهای را ارائه میدهند. در این راستا، روشهای مکانیکی بهویژه از جمله مؤثرترینها محسوب میشوند.
روشهای متداول استفاده شده در صنعت
تعدادی از تکنیکهای مدیریت تنش که تاکنون در صنایع مختلف مثل ساخت سازهها، ماشینآلات و وسایل نقلیه نصب شدهاند مورد استفاده قرار گرفتهاند. از میان آنها میتوان به موارد زیر اشاره کرد:
لایه شات پینینگ:
این روش با ایجاد پوششی محافظ و تغییر خواص سطحی قطعات، باعث کاهش تنشهای باقیمانده و بهبود عمر مفید آنها میشود.لیزر پینینگ:
استفاده از لیزر در بهینهسازی سطح قطعات، هم بهدلیل دقت بالا و هم به دلیل توانایی کنترل دقیق فرآیند، نتایج مطلوبی در کاهش تنشهای سطحی ارائه میدهد.شات پینینگ التراسونیک:
به عنوان یک روش نوین و غیر معمول، شات پینینگ التراسونیک در آزمایشهای اولیه بر روی آلیاژهای تیتانیوم با موفقیت قابل توجهی مواجه شده است. این تکنیک که گاهی به آن پینینگ التراسونیک پین چرخشی (RPUP) نیز گفته میشود، در صنایع خودرو و هوافضا کاربردهای عملی فراوانی پیدا کرده است.
مزایای استفاده از روشهای مکانیکی
سادگی و هزینه پایین:
یکی از بزرگترین مزایای استفاده از روشهای مکانیکی، سهولت اجرا و کاهش هزینههای عملیاتی است.کارایی بالا:
این روشها توانستهاند در کاهش تنشهای سطحی و بهبود خواص مکانیکی قطعات، خصوصاً در قطعات نصبشده در سازهها و وسایل نقلیه، عملکرد قابل توجهی داشته باشند.انعطافپذیری:
امکان استفاده از این تکنیکها در قطعات مختلف از جمله سازههای موجود و تجهیزات نصبشده، کاربرد آنها را در صنایع مختلف افزایش داده است.
با بهرهگیری از روشهای نوین مانند لایه شات پینینگ، لیزر پینینگ و شات پینینگ التراسونیک، صنایع مختلف قادر خواهند بود بهطور مؤثر تنشهای باقیمانده را مدیریت نموده و از این طریق عمر مفید و عملکرد سازهها، ماشینآلات و وسایل نقلیه را بهبود بخشند. این تکنیکها نه تنها از نظر اقتصادی مقرون به صرفه هستند بلکه کارایی و کیفیت نتایج ارائه شده توسط آنها نیز در سطح بالایی قرار دارد.
شات پینینگ
فرآیند شات پنینگ: جمعآوری، بازیافت و اثرات مکانیکی
فرآیند لایهبرداری شات بهمنظور جمعآوری شاتهای استفادهشده و استفاده مجدد از آنها، و همچنین حفظ گرد و غبار در یک کابینت ویژه انجام میشود. در این فرآیند، قطعه مورد نظر به صورت مکانیکی وارد جریان شات میشود تا تحت تأثیر برخورد شاتهای کروی قرار گیرد.
مشخصات شاتها
شاتها به شکل کروی بوده و از مواد و اندازههای مختلف، از 0.18 تا 2.4 میلیمتر در قطر، تهیه میشوند. دستهبندی شاتها به شرح زیر است:
فولاد پر کربن (SAEJ827)
فولاد کم کربن (SAEJ2175)
چدن
سیم برش (SAEJ441)
توپهای سخت شده (AMS 241/5)
پودر فولاد اتمیزه شده
دانههای شیشه (SAEJ 1173)
مهرههای سرامیکی (SAEJ8)
سرعت ضربه در این فرآیند بین 20 تا 150 متر بر ثانیه متغیر است.
انواع ماشینآلات مورد استفاده در شات پنینگ
سه نوع اصلی ماشین جهت انجام فرآیند شات پنینگ وجود دارد:
ماشینهای پنوماتیکی
ماشینهای گریز از مرکز
ماشینهای دوغاب بخار
این دستهبندی امکان انتخاب مناسبترین ماشین بر اساس نوع ماده و ویژگیهای شات را فراهم میکند.
دینامیک برخورد و ایجاد تنشهای پسماند
هنگام برخورد شات با سطح، به دلیل تغییر شکل پلاستیک ایجاد شده، یک گودی در سطح شکل میگیرد. پس از برگشت شات، ناحیه تغییر شکل یافته سعی در انبساط دارد؛ اما مواد احاطهکننده این انبساط را مهار کرده و تنش پسماند فشاری ایجاد میکنند. میزان تنش پسماند به عوامل زیر وابسته است:
نیروی دینامیکی وارده بر شاتها
زمان نوردهی (زمان تماس)
سختی نسبی بین شاتها و ماده آزمایششده
اندازه ضربه
برای هر ماده شرایط خاصی برای شات پنینگ وجود دارد که بهترین بهبود خواص مواد را تضمین کند. با توجه به این نکته، زمان طولانی در فرآیند شات پنینگ میتواند بهطور معکوس بر خستگی قطعه تأثیر منفی داشته باشد.
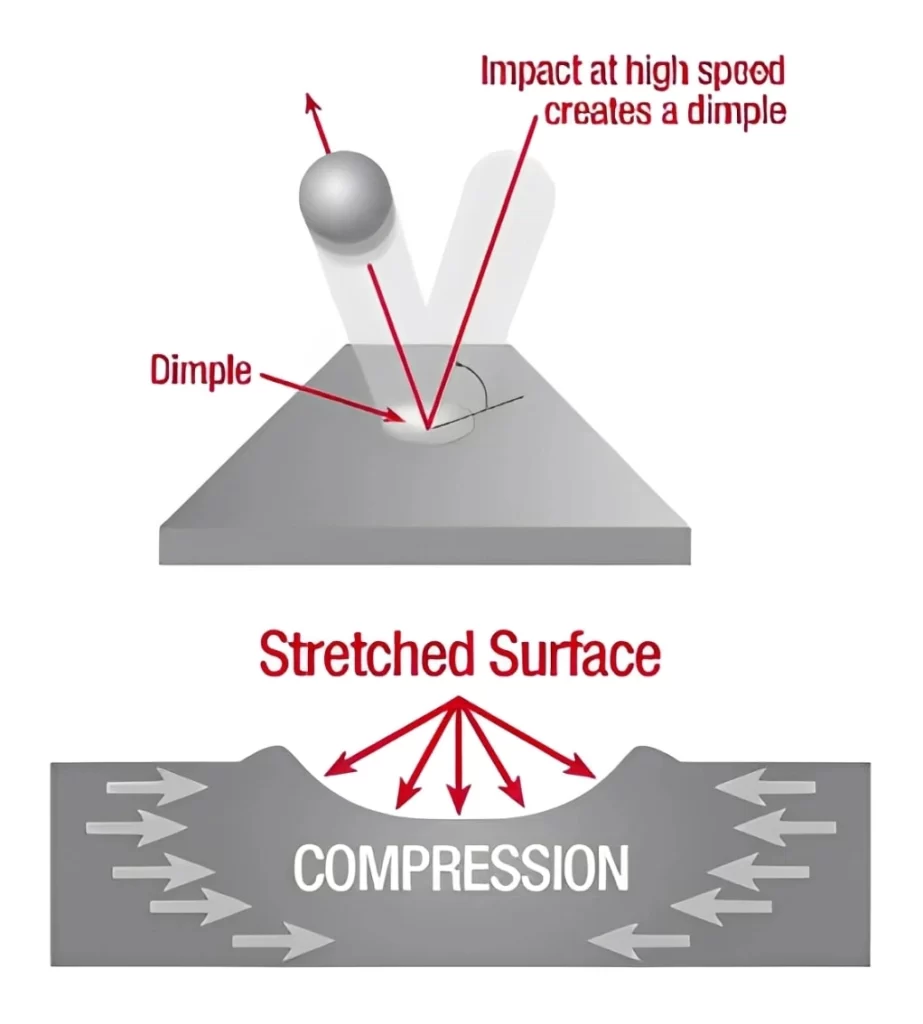
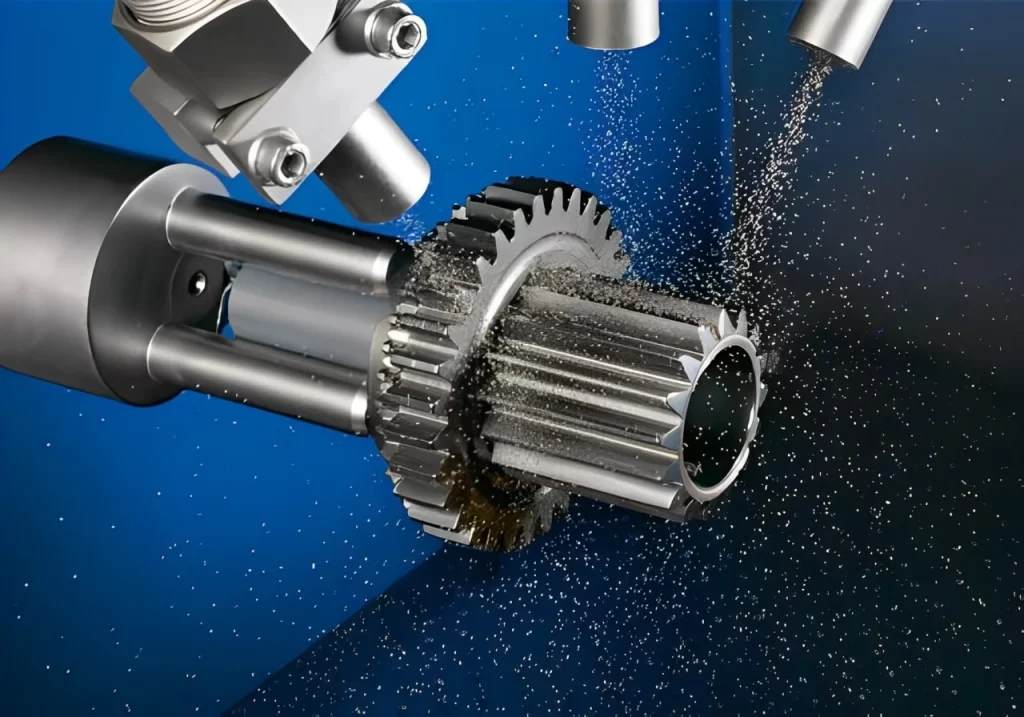
شات پینینگ التراسونیک
شات پینینگ التراسونیک (USSP) روشی است که در اصول خود مشابه شات پینینگ عمل میکند، اما با استفاده از انرژی فراصوت با فرکانس بالا، قابلیت ایجاد تغییر شکل پلاستیک و نانوبلور شدن سطح را داراست. هدف اصلی این روش القای تنش فشاری بر روی سطح قطعه جهت بهبود خواص مکانیکی و مقاومت در برابر خستگی میباشد.
ویژگیهای شات پینینگ التراسونیک
انرژی فراصوت با فرکانس بالا:
با بهرهگیری از انرژی فراصوت، برخورد سطحی شاتهای کروی انجام شده و تغییر شکل پلاستیکی دقیقتری بر روی سطح قطعه ایجاد میشود.اندازه و شکل شات:
در این روش از شاتهای بزرگتر (بین 0.4 تا 3 میلیمتر) استفاده میشود که نسبت به شات پینینگ سنتی دارای شلیک سختتر، کاملاً کروی و یکنواخت هستند.سرعت شلیک:
سرعت شلیک شاتها در محدوده 5 تا 20 متر بر ثانیه تنظیم میشود که باعث ایجاد اثرات مکانیکی مطلوب و القای تنش فشاری بیشتر بر روی سطح میگردد.
مزایا و کاربردهای شات پینینگ التراسونیک
سطح صافتر:
به دلیل استفاده از شاتهای بزرگتر و سختتر، سطح پس از انجام شات پینینگ التراسونیک صافتر و یکنواختتر نسبت به سایر روشهای مشابه به نظر میرسد.تنش فشاری بالا:
این روش منجر به القای تنش فشاری بیشتری نسبت به روشهای مرسوم میشود که نقش مهمی در بهبود مقاومت قطعه در برابر خستگی و افزایش عمر مفید آن دارد.عدم نیاز به کابینت و گردگیر:
شات پینینگ التراسونیک به عنوان یک روش دستی و قابل حمل، بدون نیاز به تجهیزات بزرگ مانند کابینتهای گردگیر، قابلیت اجرا در محلهای مختلف از جمله خطوط تولید را داراست.کاربرد در صنایع مختلف:
این تکنیک در صنایع هوافضا، خودروسازی، نیروگاهها و سایر زمینههای صنعتی مورد استفاده قرار میگیرد؛ به دلیل مزایایی مانند کاهش هزینه، انعطافپذیری و قابلیت حمل تجهیزات.
با استفاده از روش شات پینینگ التراسونیک (USSP)، صنایع مختلف قادرند با القای تنشهای فشاری بهبود یافته، سطح قطعات را تقویت کرده و مقاومت در برابر خستگی را به طور چشمگیری افزایش دهند. این تکنیک به دلیل سادگی اجرا، تجهیزات قابل حمل و نتایج دقیق، یک انتخاب ایدهآل برای برنامههای بهبود عملکرد سازهای محسوب میشود.
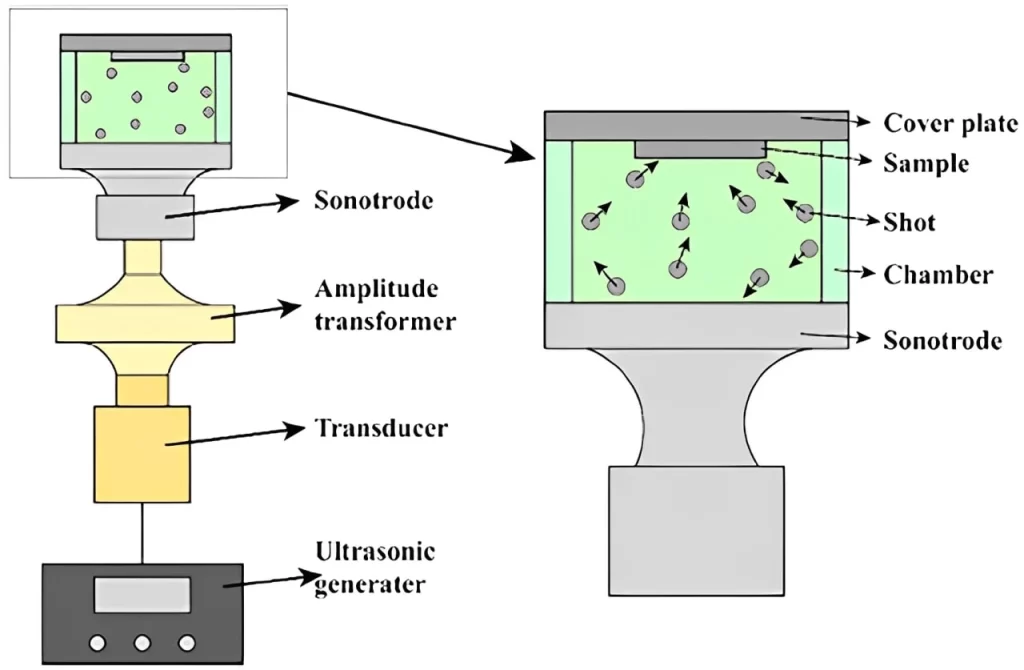
لیزر شات پینینگ (LSP)
لیزر شات پینینگ (LSP) نشان داده است که میتواند تنش پسماند فشاری بیشتری را روی سطح قطعه ایجاد کند، بدون آنکه تغییرات قابلتوجهی در پایان سطح یا شکل اجزا بوجود آید. کنترل پارامترهای این فرآیند نسبت به شات پینینگ سادهتر است و مزایای متعددی در جهت بهبود خواص سطحی ارائه میدهد.
ویژگیهای اصلی LSP
تنش پسماند فشاری بالا:
LSP به ایجاد تنش پسماند فشاری بیشتر در عمق سطح کمک میکند؛ به طوری که عمق تنشهای ایجاد شده ممکن است تا چندین میلیمتر برسد.پایان سطح بهینه:
اصلاح سطح لیزری منجر به ایجاد یک لایه ساختاری ریز دانه، تخلخل کم و سطحی نسبتاً صاف میشود. این ویژگی باعث حذف زبریهای سطحی و کاهش نقاط شروع ترک میگردد.سهولت کنترل فرآیند:
تنظیم پارامترهای LSP (مانند زمان پالس و انرژی هر پالس) به نسبت روشهای مکانیکی سنتی، سادهتر بوده و امکان بهینهسازی دقیقتر سطح را فراهم میکند.
روند انجام فرآیند LSP
این فرآیند مکانیکی با استفاده از یک پرتو لیزر با پالس بسیار کوتاه انجام میشود که مشخصات آن به صورت زیر است:
پالس لیزری:
مدت زمان پالس بین 15 تا 30 نانوثانیه.طول موج:
حدود 1.06 میکرومتر.انرژی پالس:
حداقل 50 ژول یا بیشتر در هر پالس.
برای اجرای موفق فرآیند، سطح مورد درمان باید دارای پوشش مناسبی باشد:
لایه جاذب:
سطح باید با یک لایه جاذب مانند رنگ سیاه پوشانده شود.لایه شفاف:
روی پوشش جاذب، از یک لایه شفاف (مانند آب مقطر) استفاده میشود. در نتیجه یک فعل و انفعالی بین فازهای جامد و مایع بوجود میآید که نقش مهمی در انتقال انرژی لیزر به سطح دارد.
عملکرد LSP در آلیاژهای آلومینیومی
در آلیاژهای آلومینیوم مانند A356، A112Si، 6061-T6، 7075 و 2024، فرآیند LSP توانسته است تنشهای فشاری بزرگتر و عمیقتری نسبت به روش شات پینینگ معمولی ایجاد کند. بهطور مثال:
افزایش میزان سطوح سخت شده:
در این آلیاژها، سطحهای سخت شده حاصل از LSP بیش از 50 درصد از سطحهای به دست آمده توسط شات پینینگ (SP) افزایش دارند.یگانگی فرورفتگی سطحی:
LSP باعث ایجاد یک فرورفتگی یکنواخت در امتداد سطح میشود و سطح صافتری نسبت به SP ایجاد میکند، که به کاهش احتمال شروع ترک کمک میکند.
کاربرد نهایی LSP
یکی از مزایای عمده LSP این است که میتوان از آن به عنوان یک درمان نهایی پس از جوشکاری استفاده نمود. به عنوان مثال، در یک ناحیه جوش با روش جوشکاری اغتشاشی اصطکاکی (FSW) در آلیاژ آلومینیوم 7075-T7351، آزمایشات نشان دادهاند که استفاده از LSP منجر به حذف تنشهای پسماند کششی (ضررآور در فرآیند جوشکاری) شده و بهبود قابلتوجهی در طول عمر خستگی قطعه به همراه دارد.
با بهکارگیری روش لیزر شات پینینگ، صنایع میتوانند علاوه بر افزایش تنش پسماند فشاری مطلوب، سطحی صاف و یکنواخت ایجاد کرده و از این طریق مقاومت در برابر خستگی را بهبود دهند؛ نتیجهای که به کاهش هزینهها و افزایش دوام قطعات در کاربردهای صنعتی و هوافضا منجر میشود.
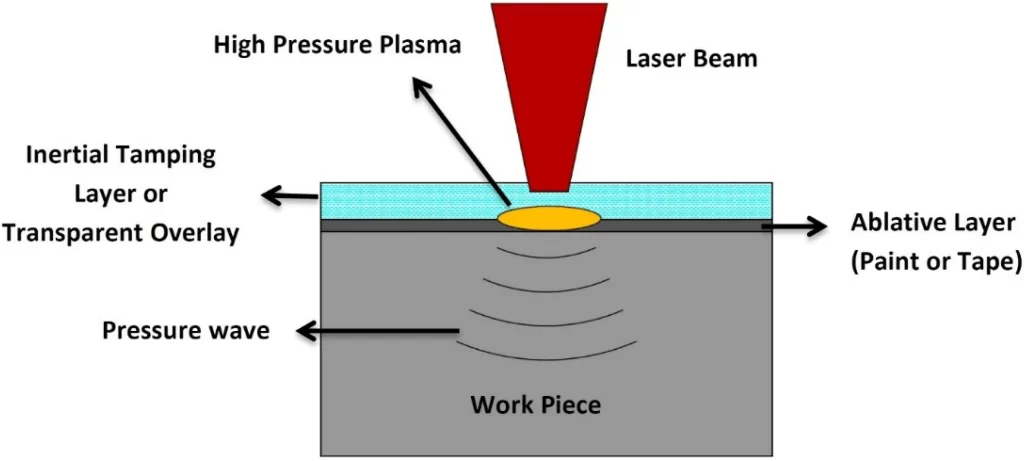