طراحی هورن برای جوش التراسونیک
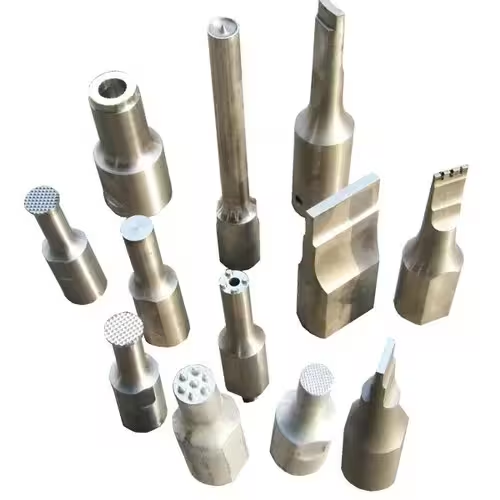
هورن دستگاه التراسونیک چیست؟
هورن (Horn) قطعهای فلزی با تراشکاری دقیق است که عمل نهایی جوش التراسونیک را انجام میدهد. به این صورت که انرژی الکتریکی توسط ژنراتور به پیزو الکتریک که بر روی ترانسدیوسر نصب شده منتقل شده، و به انرژی فراصوت تبدیل میگردد. خروجی این انرژی التراسونیک یا فراصوت هورن میباشد.
اصول التراسونیک
تعریف فرآیند:
مونتاژ پلاستیک التراسونیک فرآیندی برای اتصال یا اصلاح ترموپلاستیک ها با استفاده از گرمای تولید شده از ارتعاشات مکانیکی فرکانس بالا است. انرژی الکتریکی به ارتعاشات با فرکانس بالا تبدیل میشود که باعث ایجاد گرمای اصطکاکی در ناحیه مفصل میشود. پلاستیک در ناحیه مفصل ذوب میشود و یک پیوند مولکولی بین اجزای پلاستیکی ایجاد میکند. ارتعاشات صوتی با فرکانس بالا باعث افزایش دما میشود و باعث میشود که مواد ذوب شوند و یا به قسمت مجاور متصل شوند یا شکل ابزار را به خود بگیرند. تفاوت اصلی بین مونتاژ التراسونیک و جوشکاری یا شکلدهی حرارتی این است که چگونه گرما به محل مورد نظر وارد میشود، زیرا امواج فراصوت ارتعاشات صوتی با فرکانس بالا را منتقل میکند که از طریق ماده عبور میکند و باعث ایجاد گرما در خود ماده میشود.
مونتاژ التراسونیک چگونه انجام میشود؟
مونتاژ التراسونیک با استفاده از مبدل پیزوالکتریک و اعمال نیرو بر روی قطعات، انرژی الکتریکی با فرکانس بالا را به حرکت مکانیکی با فرکانس بالا تبدیل میکند و باعث ذوب شدن پلاستیک و ایجاد پیوند مولکولی بین اجزا میشود. فرآیند مونتاژ التراسونیک با سرد شدن پلاستیک منجر به پیوند همگن بین قطعات میشود.
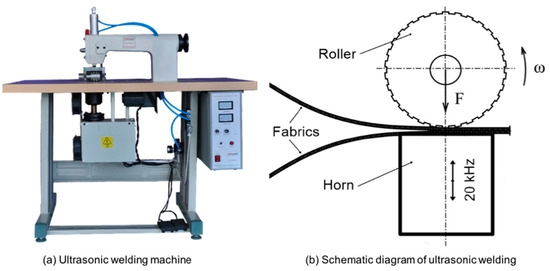
جوشکاری التراسونیک:
جوشکاری التراسونیک رایجترین کاربرد مونتاژ التراسونیک است. در جوشکاری التراسونیک، انرژی ارتعاشی با فرکانس بالا از یک شیپور همراه با فشار به قطعه کار اعمال میشود که باعث میشود ناحیه اتصال بین دو قسمت به دلیل گرمای اصطکاکی گرم شود. مواد پلاستیکی ذوب میشوند و با توقف ارتعاش قطعات به یکدیگر متصل میشوند و پلاستیک جامد میشود. فرآیند جوشکاری التراسونیک برای اتصال دو قطعه ترموپلاستیک به یکدیگر با اعمال فشار کنترل شده به قطعات و ارتعاش هورن آلومینیومی تیتانیوم یا روکش شده به صورت عمودی برای تولید گرمای اصطکاکی در سطح مشترک استفاده میشود. پلاستیک ذوب میشود و سپس اجازه داده میشود تا خنک شود، و نیروی گیره در طول زمان نگهداری حفظ میشود تا استحکام و هرمتیکی مفصل بهبود یابد. هنگامی که پلاستیک ذوب شده جامد شد، نیروی گیره برداشته میشود و دو قسمت به صورت یکپارچه به هم متصل میشوند.
مزایای مونتاژ التراسونیک:
مونتاژ التراسونیک دارای مزایای بیشماری از جمله فرآیند سریع، تمیز، کارآمد و قابل تکرار است که پیوندهای قوی و یکپارچه ایجاد میکند. این فرآیند حداقل انرژی مصرف میکند و نیازی به حلال، چسب، اتصالدهندههای مکانیکی یا حرارت خارجی ندارد. این فرآیند سازگار و همهکاره است، با توانایی تغییر سریع ابزار و قابل استفاده برای مواد دشوار. سرمایهگذاری کمهزینه در تجهیزات التراسونیک همراه با قابلیت اطمینان، عمر طولانی و عملکرد ثابت آن را به روش مونتاژ ترجیحی تبدیل میکند. مونتاژ التراسونیک به طور گسترده در صنایع مختلف از جمله خودروسازی، پزشکی، برق و الکترونیک، ارتباطات، لوازم خانگی، محصولات مصرفی، اسباببازیها، و نساجی و بستهبندی استفاده میشود. این میتواند به طور قابلتوجهی تولید را افزایش دهد و هزینههای مونتاژ را کاهش دهد.
اجزاء و توابع سیستم:
چهار جزء اصلی یک سیستم مونتاژ التراسونیک عبارتند از: ژنراتور (منبع تغذیه)، مبدل (مبدل)، تقویتکننده و بوق (ابزار صوتی). ژنراتور توان الکتریکی استاندارد را در فرکانس مورد نیاز سیستم (معمولاً 15، 20، 30 یا 40 کیلوهرتز) به انرژی الکتریکی تبدیل میکند. سپس انرژی الکتریکی به مبدل فرستاده میشود که آن را به ارتعاشات مکانیکی تبدیل میکند. برای تکمیل سیستم مونتاژ التراسونیک به پرس و فیکسچر نیز نیاز است، اما جزء اصلی محسوب نمیشوند. این فرآیند انعطافپذیر و کارآمد است و پیوندهای انتگرال قوی ایجاد میکند در حالی که انرژی بسیار کمی مصرف میکند. تقویتکننده برای افزایش یا کاهش دامنه ارتعاشات برای مطابقت با کاربرد مورد نیاز استفاده میشود. مقدار افزایش یا کاهش به صورت بهره بیان میشود که نسبت دامنه خروجی به دامنه ورودی است. سپس ارتعاشات به یک هورن با اندازه و شکل مناسب منتقل میشود تا انرژی ارتعاشی را به قطعه کار برساند. بوق ممکن است دامنه ارتعاشات را بیشتر افزایش دهد.
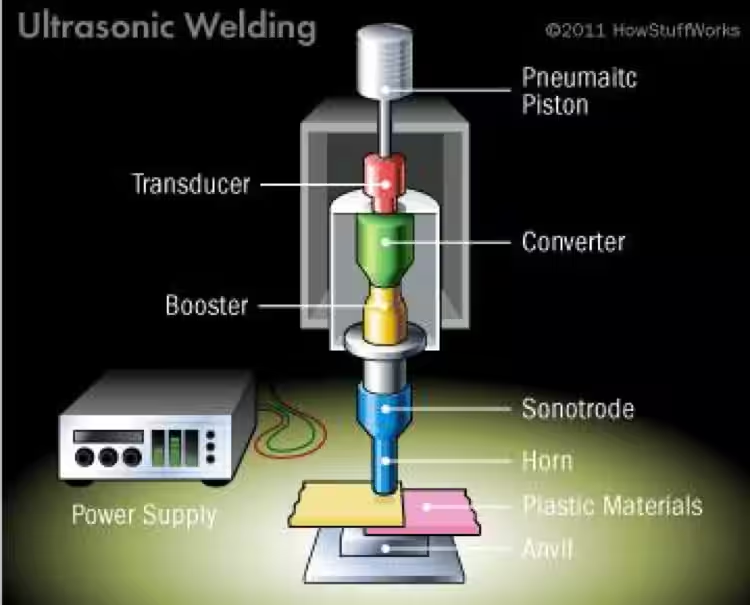
تکنیکهای استفاده از انرژی در کار:
نوع سیستم مونتاژ پلاستیک التراسونیک مورد استفاده بستگی به کاربرد دارد، با گزینههایی از سیستمهای تبدیل دستی پروب، سیستمهای پرس برای کاربردهای مهمتر، سیستمهای جابجایی قطعات شاخص چرخشی برای سرعتهای تولید بالا، واحدهای التراسونیک با مجموعههای پشتهای برای مونتاژ با سرعت بسیار بالا و رانشگرها برای نصب سفارشی که در آن سیستم پرس ممکن است خیلی بزرگ باشد. هر نوع سطوح مختلف کنترل، تکرارپذیری و سهولت استفاده را برای نیازهای مختلف تولید ارائه میدهد. سیستمهای مختلف در تصویر نشان داده شده است.
مواد پلاستیکی:
پلیمرها ترکیبات شیمیایی هستند که از ترکیب دو یا چند عنصر در یک مولکول بزرگ به وجود میآیند. دو نوع پلیمر وجود دارد: ترموست و ترموپلاستیک. ترموستها برای مونتاژ التراسونیک مناسب نیستند زیرا سخت و شکننده هستند، در حالی که ترموپلاستیکها ایدهآل هستند زیرا میتوانند در هنگام گرم شدن نرم شوند. ترموپلاستیکها به دو دسته آمورف یا نیمه کریستالی طبقهبندی میشوند که ساختار مولکولی آن خواص فیزیکی و ویژگیهای ذوب و جوش را تعیین میکند. شکل ساختار مولکولی مواد آمورف و نیمه کریستالی را نشان میدهد. ترموپلاستیکهای آمورف فرآیند نرم شدن تدریجی دارند، در حالی که مواد نیمه کریستالی دارای نقطه ذوب تیز هستند. جوشکاری مواد نیمه کریستالی نسبت به مواد آمورف دشوارتر است زیرا نیاز به انرژی بالایی برای ذوب دارند و توانایی جذب انرژی ارتعاشی دارند. تصویر تفاوت حالتهای مذاب را برای مواد آمورف و نیمه کریستالی نشان میدهد.
سازگاری مواد:
هنگام اتصال دو قطعه ترموپلاستیک، مهم است که مواد دارای خواص شیمیایی سازگار باشند. اگر مواد از نظر شیمیایی سازگار نباشند، حتی اگر با هم ذوب شوند، پیوند مولکولی وجود نخواهد داشت. بهعنوان مثال، پلی اتیلن و پلی پروپیلن را نمیتوان به یکدیگر جوش داد. به همین ترتیب، تنها پلیمرهای آمورف مشابه شانس خوبی برای جوش دادن به یکدیگر دارند، در حالی که مواد نیمه کریستالی را فقط میتوان به خود جوش داد. عوامل دیگری مانند رطوبت سنجی، عوامل آزاد کننده قالب و پرکنندهها نیز میتوانند بر جوشپذیری قطعات تأثیر بگذارند.
این تمایل یک ماده به جذب رطوبت است که بر جوشپذیری قطعات ترموپلاستیک تأثیر میگذارد. موادی مانند پلی آمید، پلی کربنات، آلیاژ پلی کربنات/پلی استر و پلی سولفون رطوبت سنجی هستند و بنابراین، اگر قطعات مرطوب جوش داده شوند، آب محبوس شده در داخل مواد زمانی که دما به نقطه جوش برسد، میجوشد و یک حالت کف در سطح مشترک ایجاد میکند. دستیابی به مهر و موم هرمتیک را دشوار میکند و استحکام پیوند را به خطر میاندازد. برای جلوگیری از این مسائل، قطعات رطوبت سنجی باید بلافاصله پس از قالبگیری جوش داده شوند یا در کیسههای پلی اتیلن با یک ماده خشککننده برای محافظت در برابر رطوبت نگهداری شوند.
عوامل رهاسازی قالب:
استفاده از عوامل آزاد کننده قالب بر روی قطعات قالبگیری شده میتواند بر جوشکاری تأثیر منفی بگذارد، زیرا اصطکاک سطحی بین قطعات را کاهش میدهد و آلودگی شیمیایی رزین میتواند از تشکیل پیوند جلوگیری کند. بهترین انتخاب برای عوامل رهاسازی قالب، نمرات قابل رنگ/چاپ هستند زیرا کمترین تداخل را با مونتاژ التراسونیک دارند و اغلب نیازی به تمیز کردن قبل از مونتاژ ندارند. در صورت امکان از استئارات روی، استئارات آلومینیوم، فلوروکربنها و سیلیکونها اجتناب شود زیرا برای مونتاژ التراسونیک مضر هستند.
روانکنندهها:
استفاده از روانکنندههایی مانند موم، استئارات روی، اسید استئاریک، استئارات آلومینیوم و استرهای چرب میتواند تأثیر منفی بر فرآیند پیوند التراسونیک داشته باشد. این روانکنندهها جریان رزین را بهبود میبخشند، اما از آنجایی که نمیتوانند حذف شوند و اصطکاک را در رابطهای اتصال کاهش دهند، میتوانند کل فرآیند التراسونیک را شکست دهند. نرمکنندهها انعطافپذیری و نرمی مواد را افزایش میدهند، اما میتوانند در طول زمان به دلیل مهاجرت، پیوند یا اتصال را ضعیف کنند. نرمکنندههای مورد تأیید FDA ترجیح داده میشوند، اما آزمایش قبل از تولید توصیه میشود.
پرکنندهها:
پرکنندههایی مانند الیاف شیشه، تالک، فیبر کربن و کربنات کلسیم برای تغییر خواص فیزیکی به رزینها اضافه میشوند. پرکنندههای معدنی رایج میتوانند با بهبود انتقال انرژی ارتعاشی، جوشپذیری ترموپلاستیکها را افزایش دهند. با این حال، یک رابطه مستقیم بین افزودن پرکننده و جوشپذیری فقط در یک محدوده خاص وجود دارد. محتوای پرکننده بیش از حد میتواند منجر به تراکم در محل اتصال شود و دستیابی به یک جوش ثابت را دشوار کند و همچنین میتواند باعث سایش بیش از حد ابزار شود و به تجهیزات التراسونیک قویتری نیاز داشته باشد.
بازدارندههای شعله:
مواد بازدارنده شعله به پلاستیکها اضافه میشوند تا خاصیت اشتعالپذیری آنها را تغییر دهند و از احتراق جلوگیری کنند. با این حال، این کندکنندهها میتوانند استحکام اتصال نهایی را در جوشکاری ترموپلاستیک تضعیف کنند و برای دستیابی به استحکام کافی نیاز به استفاده از تجهیزات پرقدرت دارند که در دامنههای بالاتر کار میکنند.
Regrind:
Regrind به مواد پلاستیکی بازیافتی یا فرآوری شده اشاره دارد که به رزین اصلی اضافه میشود. مونتاژ التراسونیک امکان استفاده از regrind را بدون وارد کردن هیچ ماده خارجی میدهد. با این حال، برای دستیابی به بهترین نتایج، توصیه میشود که درصد آسیاب مجدد را پایین نگه دارید و مطمئن شوید که پلاستیک تخریب یا آلوده نشده است.
رنگها:
افزودن رنگها یا رنگدانهها به پلاستیک تأثیر قابلتوجهی بر جوشپذیری مواد نمیگذارد، مگر زمانی که نسبت رنگکننده به رزین بیش از حد بالا باشد. قسمتهای سفید و سیاه ممکن است به رنگدانههای بیشتری نیاز داشته باشند و رنگهای مختلف همان قسمت ممکن است به پارامترهای تنظیم متفاوتی نیاز داشته باشد. توصیه میشود قبل از تولید کامل رنگدانهها را آزمایش کنید.
درجه رزین:
درجه رزین مورد استفاده در یک برنامه کاربردی میتواند به طور قابلتوجهی بر جوشپذیری آن تأثیر بگذارد. درجههای مختلف از یک ماده میتواند دمای مذاب متفاوتی داشته باشد که منجر به جوش ضعیف یا مشکلات سازگاری شود. توصیه میشود برای بهترین نتیجه در مونتاژ التراسونیک از مواد همدرجه استفاده کنید.
طراحی مفصل و قطعه
نیازهای اساسی:
طراحی قطعات جفتگیری در مونتاژ برای دستیابی به نتایج مطلوب بسیار مهم است. طرحهای اتصال متفاوتی وجود دارد که هر کدام مزایای خود را دارند و انتخاب یک طرح خاص به عواملی مانند نوع پلاستیک، هندسه قطعه و نیازهای جوش بستگی دارد.
سه شرط اساسی در طراحی اتصال
1. یک منطقه تماس یکنواخت
2. یک منطقه تماس اولیه کوچک
3. یک وسیله تراز
یک منطقه تماس یکنواخت تضمین میکند که سطوح جفتگیری در تماس کامل با محل اتصال هستند و در صورت امکان اتصال باید در یک صفحه باشد. یک منطقه تماس اولیه کوچک انرژی و زمان لازم برای شروع و تکمیل ذوب بین قطعات جفتگیری را به حداقل میرساند. وسیلهای برای تراز از ناهماهنگی در حین عملیات جوشکاری جلوگیری میکند و میتواند از طریق پینها، سوکتها، کانالها و زبانههای همترازی قالبگیری شده به دست آید. در فرآیند جوش اولتراسونیک، استفاده صحیح از هورن برای توزیع یکنواخت انرژی و تراز دقیق قطعات اهمیت بالایی دارد. بهتر است از بوق و/یا فیکسچر برای تراز استفاده نکنید. اتصال لب به لب صاف، که فقط در نقاط بالا جوش میخورد، منجر به جوشهای ناسازگار و نامنظم میشود. افزایش زمان جوش، نقاط جوش اصلی را بزرگ میکند و باعث فلاش بیش از حد در خارج از محل اتصال میشود که در شکل نیز نشان داده شده است. رساندن یکی از سطوح به یک نقطه جوشهایی ایجاد میکند که ظاهر خوبی دارند اما استحکام کمی دارند. هنگامی که استحکام بهبود مییابد، فلاش بیش از حد ظاهر جوش را خراب میکند. شکل مشکلاتی را که در قطعات دیوار نوک تیز با آن مواجه میشود نشان میدهد.
مدیریت انرژی:
مدیر انرژی یک مهره مثلثی شکل است که در رابط مشترک قالبگیری شده است که حجم خاصی از مواد را برای ذوب فراهم میکند و در نتیجه استحکام پیوند خوبی را بدون فلاش بیش از حد ایجاد میکند. این طرح اتصال برای پلیمرهای آمورف توصیه میشود. مدیر انرژی انرژی مافوق صوت را در رأس متمرکز میکند و باعث ایجاد سریع گرما و ذوب شدن مواد میشود که پیوند مولکولی را با سطح جفتگیری تشکیل میدهد. این طرح اتصال برای رزینهای آمورف توصیه میشود زیرا توانایی آن در ایجاد پیوند مولکولی و دستیابی به سطح تماس اولیه کوچک، یک منطقه تماس اولیه یکنواخت و کوچک را فراهم میکند.
اتصال لب به لب با یک مدیر انرژی:
اتصال لب به لب با یک مدیر انرژی به دلیل توانایی آن در ایجاد پیوند مولکولی و دستیابی به سطح تماس اولیه کوچک، طراحی مناسبی برای رزینهای آمورف در جوشکاری التراسونیک است. با این حال، برای رزینهای نیمه کریستالی ایدهآل نیست، زیرا مواد جابجا شده از مدیر انرژی اغلب قبل از جاری شدن در سراسر اتصال، جامد میشوند و باعث کاهش استحکام و سخت شدن آببندی هرمتیک میشوند. شکل مدیر انرژی رزینهای آمورف و نیمه کریستالی را نشان میدهد. هنگامی که یک مدیر انرژی باید با رزینهای نیمه کریستالی استفاده شود، طراحی بزرگتر و شیبدارتر برای قرار دادن در سطح جفتگیری توصیه میشود که انجماد و تخریب زودرس را کاهش میدهد.
اتصال پلهای:
اتصال پلهای نوعی از طراحی مشترک مدیر انرژی است که دو مورد از الزامات اساسی طراحی اتصال را برآورده میکند: سطح تماس یکنواخت و سطح تماس اولیه کوچک. یک مفصل پلهای نیز تراز را فراهم میکند. استحکام اتصال پله کمتر از اتصال لب به لب با یک مدیر انرژی است و حداقل ضخامت دیواره توصیه شده 0.080 تا 0.090 اینچ است. اتصال پلهای زمانی استفاده میشود که ظاهر زیبایی مجموعه مهم باشد، زیرا فلاش را در قسمت بیرونی از بین میبرد و یک اتصال قوی ایجاد میکند. ارتفاع و عرض زبانه در محل اتصال پله باید هر کدام یک سوم ضخامت دیوار باشد و عرض شیار باید کمی بیشتر باشد تا از عدم تداخل اطمینان حاصل شود. عمق شیار باید کمی بیشتر از ارتفاع زبانه باشد تا فاصله کمی بین قسمتهای تمامشده برای اهداف آرایشی ایجاد شود.
مفصل زبانه و شیار:
مفصل زبانه و شیار نوع دیگری از اتصال مدیر انرژی است. این سه الزام طراحی مفصل را برآورده میکند: یک منطقه تماس یکنواخت، یک منطقه تماس اولیه کوچک و یک وسیله تراز، و همچنین از فلاش در دو طرف رابط جلوگیری میکند. این اتصال برای کاربردهایی که مکانیابی خود و جلوگیری از فلاش مهم است و برای آببندی هرمتیک فشار پایین ایدهآل است. با این حال، پتانسیل کمتری برای استحکام جوش در مقایسه با سایر طرحهای اتصال دارد و حداقل ضخامت دیواره 0.120 تا 0.125 اینچ توصیه میشود. مدیر انرژی همان چیزی است که در مفصل باسن استفاده میشود. زبانه باید یک سوم ارتفاع دیوار باشد و فاصله باید در هر طرف حفظ شود تا مواد مذاب جریان یابد. شیار باید 0.004 تا 0.008 اینچ پهنتر از زبانه و 0.005 اینچ تا 0.010 اینچ عمق کمتری داشته باشد. فاصله کمی بین قطعات تمامشده برای اهداف آرایشی باقی میماند.
مفصل برشی:
اتصال برشی زمانی مورد استفاده قرار میگیرد که به یک مهر و موم قوی هرمتیک نیاز باشد و برای رزینهای نیمه کریستالی مناسب است. مقدار معینی از تداخل در قطعه برای انجام جوش طراحی شده است. عمل لکهدار شدن دو سطح ذوب شده در سطح مشترک جوش، نشتی، حفرهها و قرار گرفتن در معرض هوا را از بین میبرد و در نتیجه یک جوش ساختاری قوی ایجاد میکند. برای ایجاد تکیهگاه صلب از دیواره جانبی و جلوگیری از انحراف قطعه در حین جوشکاری، یک یراق ضروری است. فیکسچر باید با شکل قطعه مطابقت داشته باشد و برای برداشتن آسان شکافته شود. اتصال برشی سه الزام طراحی اتصال را برآورده میکند: لید-این همترازی و مکان خود را فراهم میکند، قطعات طراحی شده و قالبگیری شده به درستی سطح تماس یکنواخت را تضمین میکنند و سطح تماس اولیه کوچک در پایه لید به وجود میآید.
طراحی قطعات:
در طراحی قطعات باید فاکتورهای مختلفی فراتر از طراحی اولیه مفصل در نظر گرفته شود.
جوشکاری میدان نزدیک در مقابل میدان دور:
محل اتصال نسبت به ناحیه تماس هورن در کاربردهای جوشکاری التراسونیک حیاتی است. جوشکاری میدان نزدیک، که در آن فاصله بین هورن و رابط اتصال 1/4 اینچ (6 میلیمتر) یا کمتر است، نسبت به جوشکاری میدان دور ترجیح داده میشود. جوشکاری میدان دور، که به دامنههای بالاتر، زمانهای جوش طولانیتر و فشار هوای بالاتر نیاز دارد، معمولاً فقط برای رزینهای آمورف توصیه میشود که انرژی را بهتر از رزینهای نیمه کریستالی انتقال میدهند.
تماس موازی:
جوش بهینه زمانی حاصل میشود که رابط اتصال در یک صفحه موازی با سطح تماس هورن باشد. این به انرژی التراسونیک اجازه میدهد تا همان فاصله را از طریق قسمت پلاستیکی طی کند تا به مفصل برسد. علاوه بر این، سطحی که بوق با آن تماس میگیرد نیز باید روی یک صفحه موازی با اتصال قرار گیرد.
سایر ملاحظات طراحی قطعه:
گوشههای تیز:
گوشههای تیز در قطعات پلاستیکی میتواند منجر به استرس زیاد شود و احتمال شکستگی یا ذوب شدن تحت انرژی ارتعاشی التراسونیک را افزایش دهد. برای جلوگیری از این امر، داشتن شعاع سخاوتمندانه در تمام گوشهها و لبهها برای کاهش استرس توصیه میشود.
حفرهها یا محلهای توخالی:
سوراخها، حفرهها، زاویهها و خمها مانع از انتقال انرژی التراسونیک میشوند که ممکن است منجر به جوشکاری کم یا بدون جوش در این نواحی شود. برای بهینهسازی جوشکاری، زوایای تیز، خمها و سوراخها باید در صورت امکان حذف شوند.
ضمائم:
برجستگیهای روی قطعات پلاستیکی در صورت قرار گرفتن در معرض انرژی ارتعاشی میتوانند باعث استرس و تحلیل رفتن (افتادن) شوند. برای به حداقل رساندن این امر، میتوان شعاع سخاوتمندانهای را در محل اتصال اضافه کرد، میتوان نیروی سبکی برای خنثی کردن خمش اعمال کرد، زائدهها را ضخیمتر کرد، یا در صورت امکان میتوان از تجهیزات 40 کیلوهرتز استفاده کرد.
دیافراگم:
قطعات دایرهای مسطح نازک میتوانند تحت انرژی مافوق صوت خم شده و خم شوند و به دلیل گرمای تولید شده منجر به ذوب یا سوختن شوند. برای جلوگیری از این “دیافراگم”، ضخیمتر کردن مناطق آسیبدیده توصیه میشود.
سایر تکنیکهای مونتاژ:
شرطی یا چلهگذاری:
چلهگذاری فرآیند قفل مکانیکی دو قسمت به یکدیگر با ذوب و اصلاح گل میخ است. این فرآیند زمانی استفاده میشود که جوشکاری به دلیل مواد غیر مشابه امکانپذیر نباشد یا زمانی که نگهداری مکانیکی کافی باشد. استیکینگ مزایایی مانند زمان چرخه کوتاه، مجموعههای محکم، کنترل خوب فرآیند و تکرارپذیری دارد و نیاز به مواد مصرفی مانند پیچ یا چسب را از بین میبرد. رایجترین کاربرد، اتصال فلز به پلاستیک با قالبگیری یک گل میخ در قسمت پلاستیکی و سپس استفاده از یک شیپور ارتعاشی با نوک کانتور برای ایجاد گرمای موضعی و اصلاح سر گل میخ است. یکپارچگی مونتاژ ستونی به طراحی و پارامترهای التراسونیک مورد استفاده در طول فرآیند بستگی دارد، که باید سطح تماس را به حداقل برساند و انرژی را برای یک ذوب سریع و کنترلشده متمرکز کند.
سهام مشخصات روزت استاندارد:
پایه استاندارد پروفیل روزت یک طرح پایه پایه است که میتواند اکثر نیازها را برآورده کند و برای چیدن گل میخهای سر صاف با قطر 1/16 اینچ یا بزرگتر استفاده میشود. این یک سر با قطر دو برابر گل میخ اصلی ایجاد میکند و برای ترموپلاستیکهای صلب و غیر سفت توصیه میشود.
چوب گنبد:
پایه گنبدی برای گل میخهای کوچکتر یا زمانی که تراز هورن یک چالش است استفاده میشود و همچنین برای رزینهای پر از شیشه برای جلوگیری از سایش هورن توصیه میشود. انتهای گل میخ باید جهت اطمینان از یک ناحیه تماس اولیه کوچک مشخص شود و همترازی بوق و گل میخ نسبت به پایه استاندارد پروفیل روزت اهمیت کمتری دارد.
چوب توخالی:
پایه توخالی برای گل میخهای بزرگتر از 5/32 اینچ قطر استفاده میشود و به جلوگیری از فرورفتگی سطحی و حفرههای داخلی در طول قالبگیری کمک میکند. زمان چرخه التراسونیک را با ذوب و اصلاح مواد کمتر کاهش میدهد و یک سر قوی و بزرگ تولید میکند. در صورت تعمیر، میتوان با قرار دادن یک پیچ خودکار در گل میخ توخالی، سر شکل گرفته را جدا کرد و دوباره سرهم کرد.
چوب خمیده:
پایه قلاب دار روشی ساده و سریع است که میتوان آن را با تمام ترموپلاستیکها استفاده کرد. این اجازه میدهد تا چندین پایه بدون نگرانی در مورد تراز دقیق یا قطر گل میخ ساخته شود و به ظاهر اهمیتی نمیدهد.
سهام فلاش:
پایه فلاش زمانی استفاده میشود که سر گل میخ برجسته بالای سطح قسمت متصل مجاز نباشد. این به طراحی ناودانی مخروطی نیاز دارد و سوراخ در قسمتی که باید متصل شود به صورت متقابل فرو رفته است تا به گل میخ ذوب شده اجازه دهد آن ناحیه را پر کند و قسمت متصل شده را در جای خود محکم کند.
جوشکاری زائدها:
جوشکاری ناودانی التراسونیک جایگزینی برای چنگ زدن است و برای اتصال قطعات پلاستیکی از مواد مشابه در نقاط منفرد یا چندگانه استفاده میشود. در کاربردهایی که سایر تکنیکها به دلیل مواد، اندازه یا پیچیدگی امکانپذیر نیستند مفید است. در این فرآیند، یک گل میخ به داخل یک سوراخ رانده میشود و جوشکاری در امتداد محیط آن انجام میشود تا یک اتصال برشی ایجاد شود.
درج:
درج التراسونیک فرآیند تعبیه یک جزء فلزی در یک قطعه ترموپلاستیک است. یک سوراخ از قبل در قسمت ترموپلاستیک ساخته شده است که کمی کوچکتر از O.D است. از درج. انرژی التراسونیک اعمال شده به درج حرارت اصطکاکی ایجاد میکند که پلاستیک را ذوب میکند و اجازه میدهد تا درج در جای خود رانده شود. این فرآیند در کمتر از یک ثانیه کامل میشود و درج توسط پلاستیک ذوب شده احاطه میشود. از مزایای درج التراسونیک میتوان به زمان چرخه کوتاه، عدم فشار روی پلاستیک اطراف درج فلزی، عدم آسیب قالب، کاهش زمان چرخه قالبگیری، توانایی راندن چندین درج به طور همزمان و تکرارپذیری و کنترل بالا اشاره کرد.
نوسانگیری و شکلدهی:
Swaging فرآیند مونتاژ دو ماده با ذوب و اصلاح یک برآمدگی پلاستیک برای جذب جزء دیگر، معمولاً یک ماده غیر مشابه مانند شیشه است. این یک روش سریع و کارآمد برای مونتاژ بدون ایجاد پیوند مولکولی است. Swaging نیاز به ابزار ویژه و در نظر گرفتن خواص مواد درگیر دارد. شکل سوج توسط صفحه هورن تعیین میشود که نحوه ذوب شدن و جریان پلاستیک را کنترل میکند. Swage میتواند پیوسته یا قطعهبندی شده باشد. Swaging این مزیت را دارد که مونتاژ تمام شده محکم، زمان چرخه سریع، و حذف نیاز به بست یا چسب را دارد.
جوش نقطهای:
جوشکاری نقطهای التراسونیک روشی برای اتصال دو جزء ترموپلاستیک مشابه در نقاط خاص بدون سوراخ از پیش شکلگرفته یا مدیر انرژی است. این فرآیند یک پیوند قوی ایجاد میکند و میتواند بر روی قطعات بزرگ، ورقهای ترموپلاستیک و قطعاتی با اشکال پیچیده یا سطوحی که دسترسی به آنها سخت است، استفاده شود. دستورالعملهای اولیه برای جوشکاری نقطهای شامل استفاده از تکیهگاه صلب، دامنه متوسط تا زیاد و فشار کم است. جوش نقطهای را میتوان با استفاده از مبدل دستی انجام داد و یک فرآیند مونتاژ سریع و کارآمد بدون نیاز به بستهای اضافی یا اتصالات خاص است.
تنزل دادن:
جداسازی التراسونیک فرآیندی است که برای جداسازی قطعات قالبگیری تزریقی از سیستمهای رانر آنها استفاده میشود. این شامل اعمال انرژی التراسونیک به دونده به روشی خارج از فاز است که باعث ذوب شدن قطعات در دروازه میشود. بهتر است با ترموپلاستیکهای سفت و سخت مانند ABS، استایرن یا اکریلیک استفاده شود و دارای مزایایی مانند عملکرد سریع، فشار کم بر روی قطعات و شکستگی تمیز در سطح قطعه است. دستورالعملهای جداسازی التراسونیک شامل داشتن یک ناحیه دروازه کوچک و/یا نازک و داشتن تماس هورن تا حد امکان به دروازه است.
جوشکاری اسکن:
جوشکاری اسکن یک فرآیند جوشکاری التراسونیک با سرعت بالا برای قطعات ترموپلاستیک مسطح است که در زیر یک شیپور ثابت یا دوار و سندان منتقل میشوند. این میتواند برای هر دو قسمت بزرگ و کوچک با حداقل یک سطح صاف برای تماس با هورن استفاده شود و برای ترموپلاستیکهای سفت و سخت و برخی از کاربردهای پارچه یا فیلم مناسب است. طراحی مفصل باید خود مکانیابی باشد، مانند زبانه و شیار، پله، یا سنجاق و سوکت.
چسباندن و بریدن:
دو روش متداول مونتاژ التراسونیک پیوند التراسونیک و برش التراسونیک است.
اتصال التراسونیک:
باندینگ التراسونیک تکنیکی است که در صنایع نساجی، پوشاک و منسوجات برای مونتاژ دو یا چند لایه از مواد منسوج با عبور دادن آنها بین یک شیپور ارتعاشی و یک درام چرخشی استفاده میشود. حرکت مکانیکی با فرکانس بالا و نیروی فشاری بین بوق و درام گرمای اصطکاکی ایجاد میکند و مواد را در نقاط تماس شیپور/ماده به یکدیگر متصل میکند. این فرآیند به انرژی کمتری نسبت به اتصال حرارتی نیاز دارد و منجر به یک ماده نرم، قابل تنفس و جاذب میشود که برای کاربرد در صنایع پزشکی و اتاق تمیز مناسب است. در اتصال التراسونیک به هیچ مواد مصرفی، چسب یا بست نیازی نیست. شکل زیر پیوند التراسونیک را نشان میدهد.
برش التراسونیک:
برش التراسونیک فرآیندی است که برای مهر و موم کردن لبههای یک ماده ترموپلاستیک با عبور آن بین یک شیپور ارتعاشی و یک چرخ برش دوار (سندان) استفاده میشود. این فرآیند همچنین لبههای پارچههای بافتهشده را مهر و موم میکند و میتواند برای شکاف و ذوب دو یا چند لایه از مواد بافتهشده و/یا منسوجات نبافته استفاده شود. برش التراسونیک سرعت عمل بالایی دارد و بسته به نیاز و فرآیند ساخت مواد میتواند با استفاده از روش پیوسته، غوطهور یا پیمایش انجام شود.
طراحی اجزای اصلی
ژنراتورها:
ژنراتورهای التراسونیک دستگاههای الکتریکی هستند که برق AC استاندارد را دریافت کرده و در فرکانس خاصی به انرژی الکتریکی تبدیل میکنند. فرکانس خروجی میتواند از 15 کیلوهرتز تا 40 کیلوهرتز و سطوح توان خروجی تا 4800 وات باشد. ژنراتورها از یک تقویتکننده قدرت استفاده میکنند که ترانزیستورها را با سرعت 20000 یا 40000 سیکل در ثانیه روشن و خاموش میکند. این یک سیگنال پرقدرت به مبدل میفرستد، که لرزش دارد و یک سیگنال بازخورد را به شکل موج سینوسی به تقویتکننده میفرستد. در طراحیهای قبلی، یک اپراتور باید فرکانس تقویتکننده قدرت را برای مطابقت با فرکانس مبدل تنظیم میکرد. مدار شروع نرم معمولی با اعمال نیم دامنه به بار در طول دوره راهاندازی، مشکلات راهاندازی را کاهش داد، اما همچنان مشکلات ذاتی داشت. ژنراتورهای التراسونیک دارای پیشرفتهایی در طراحی هستند که مشکلات راهاندازی را کاهش میدهد و استرس را در مجموعه پشته از بین میبرد.
کنترل ریزپردازنده:
تایمر دیجیتال در سیستمهای مونتاژ التراسونیک به عنوان “مغز” سیستم عمل میکند، حرکت بالا و پایین پرس/رانشگر را کنترل میکند و انرژی التراسونیک تولید شده توسط ژنراتور را روشن و خاموش میکند. فهرستی از دستورالعملها یا حالتهایی را ذخیره میکند که میتوان آنها را برای انتخاب تغییرات در چرخه جوش با تنظیم زمان جوش، زمان نگهداری و پارامترهای سیستم تغییر داد. فناوری کنترل ریزپردازنده حالتهای عملیاتی متعددی را برای کنترل دقیق فرآیند، تکرارپذیری و سازگاری جوش ارائه میکند که در نتیجه کیفیت قطعه بهتر و قطعات رد شده کمتری به همراه دارد.
مبدلها:
مبدلها برای تبدیل انرژی الکتریکی دریافتی از ژنراتور به انرژی مکانیکی در قالب ارتعاشات عمودی با فرکانس بالا استفاده میشوند. آنها از پیزوالکتریک استفاده میکنند که با فشردهسازی یک ماده کریستالی، الکتریسیته یا قطبیت الکتریکی تولید میکند. قلب یک مبدل، عناصر سرامیکی پیزوالکتریک است که وقتی در معرض انرژی الکتریکی متناوب قرار میگیرند، منبسط و منقبض میشوند. مبدلهای التراسونیک از یک لجن پشتی فولادی، عناصر سرامیکی و یک لجن جلوی آلومینیومی تشکیل شدهاند تا حداکثر انرژی ارتعاشی را به بوستر و بوق هدایت کنند. نقطه گره، ناحیهای با حرکت خطی کمی اما انبساط و انقباض شعاعی، برای نصب مبدل در یک پوسته استفاده میشود. اگر نصب جامد مورد نظر است، میتوان از پایههای رزونانسی با دیوارههای فلزی نازک که برای ارتعاش در فرکانس طبیعی مبدل تنظیم شدهاند، استفاده کرد. با این حال، این هزینه تولید را افزایش میدهد. مبدلها فرکانسهای مختلفی با دامنههای اوج به پیک متفاوت دارند که بیشترین فرکانس آن 50 کیلوهرتز و کمترین آن 15 کیلوهرتز است. دامنه پیک به پیک از 31 میکرون (0012/0 اینچ) تا 8 میکرون (00031/0) متغیر است. از بوسترها و بوقها برای ضرب دامنه استفاده میشود تا ارتعاش لازم برای مبدل برای انجام کار مفید فراهم شود.
تقویتکنندهها:
تقویتکنندهها دو هدف اصلی را دنبال میکنند: ایجاد یک نقطه نصب دوم برای مجموعه پشته و تقویت یا کاهش دامنه. دو نوع تقویتکننده وجود دارد: تقویتکنندههای استاندارد با حلقههای نصب تقسیمشده و تقویتکنندههای تشدید ثبتشده بدون حلقههای O برای نصب ثابت. تقویتکنندهها میتوانند از تیتانیوم یا آلومینیوم ساخته شوند و در نسبتهای بهره متفاوتی ارائه شوند تا دامنه پشته را مطابق با نیاز ذوب شدن پلاستیک در هر کاربرد تنظیم کنند. اندازه تقویتکننده بهینه برای هر برنامه باید استفاده شود و تنظیم دامنه ژنراتور باید نزدیک به 100٪ باقی بماند و تنها در صورت لزوم تنظیمات کوچک انجام شود. حداکثر اندازه تقویتکننده حداکثر افزایش توصیه شده روی بوق مهر شده است.
پرس:
پرس التراسونیک دستگاهی است که انرژی مافوق صوت را بر روی قطعه کار اعمال میکند تا جوشهای منسجم و رضایتبخشی ایجاد کند. اثربخشی پرس به پایداری و قابلیت اطمینان ساختار آن بستگی دارد، به طوری که اجزای فولادی یکپارچگی ساختاری بیشتری نسبت به قطعات آلومینیومی دارند. خمش باید به حداقل برسد تا از ناهماهنگی جلوگیری شود و تعداد جوشهای رد شده کاهش یابد.
طراحی مونتاژ اسلاید:
طراحی مجموعه اسلاید در پرس التراسونیک نقش مهمی در تعیین کارایی و طول عمر دستگاه دارد. برخی از طرحها، مانند طرحهایی که بوشهای برنزی دارند، به دلیل ویژگیهای جریان سرد، میتوانند با مشکلات سایش و مهاجرت مواجه شوند. با استفاده از ابزارهای مختلف برای ثابت نگه داشتن بوشینگها و حفظ تلرانس محکم بین بوشینگ و میله میتوان از این مسائل جلوگیری کرد. اسلایدهای توپ خطی گزینهای بادوامتر و دقیقتر هستند، بدون فاصله بین بوش و میله، و اصطکاک عملیاتی را به حداقل میرساند. سیستم حرکت توپ خطی نوع ریلی این مزایا را در یک طراحی فشرده ارائه میکند و اجازه میدهد چندین سر جوش نزدیکتر به هم قرار گیرند.
نیرو:
پرس التراسونیک معمولاً با استفاده از فشار هوا از یک سیلندر هوا کار میکند که توسط یک گیج و تنظیمکننده کنترل میشود. برخی از جوشکارهای التراسونیک یک گزینه الکترونیکی برای تنظیم و نظارت بر سطوح فشار با استفاده از کنترلکننده فرآیند التراسونیک، لودسل، مبدل نیرو و تنظیمکننده فشار الکترونیکی ارائه میدهند. سرعت رو به پایین را میتوان با استفاده از فلومتر کنترل جریان هوای ورودی تنظیم کرد. نیروی اعمالشده به کار در طول فعالسازی التراسونیک و سرعت پایین آمدن هر دو میتوانند بر نتایج نهایی جوشکاری تأثیر بگذارند. پرسهای اصلی مکانیسمی برای تغییر پویای نیروی ماشه دارند.
توالی تحریک برای پرس التراسونیک:
- بوق با قطعه کار تماس پیدا میکند و باعث فشرده شدن فنرهای قالب میشود که بین اسلاید و سیلندر هوا قرار میگیرند.
- میکروسوئیچ و هدف قابل تنظیم تماس برقرار میکنند و انرژی التراسونیک را فعال میکنند.
- فنرهای قالب تضمین میکنند که با ذوب شدن مواد پلاستیکی، نیروی ثابتی به قطعه کار وارد میشود.
سیستمهای جوشکاری حلقه بسته (اولویت انرژی):
جوشکاری با اولویت انرژی با حلقه بسته، روشی برای مونتاژ پلاستیک التراسونیک است که قطعات را بر اساس میزان انرژی جذبشده، به جای مدت زمان از پیش تعیینشده، جوش میدهد. هورن پایین میآید و قطعه را لمس میکند، سپس التراسونیک روشن میشود و تا رسیدن به سطح انرژی از پیش تنظیمشده روشن میماند. پس از رسیدن به سطح انرژی، التراسونیک خاموش میشود و سر جمع میشود.
ویژگیهای سیستم التراسونیک سروو:
سیستمهای سروو جوشکار التراسونیک رویکرد متفاوتی را به تکنیکهای اتصال سنتی ارائه میدهند و با ویژگیهای ثبتشده خود، جوشهای با کیفیت بهبود یافته و نتایج ثابتی را ارائه میدهند.
- کنترل فواصل فروپاشی جوش و نگهداری: کنترل دقیقتر فواصل فروپاشی جوش و نگهداری نسبت به سیستمهای پنوماتیکی.
- تغییر سریع سرعت: سرعت تغییر سریع و قابلیت پروفایل کردن سرعت در طول جوش.
- تطبیقپذیری: سیستمهای سروو برای جوشکاریهای دشوار مناسبتر هستند و نتایج قابل تکراری ارائه میدهند.